Robot Learning
Visitors to the School of Architecture at The University of Texas at Austin may have been at first puzzled, albeit dazzled, by the sight of the exhibition that greeted them in the Mebane Gallery for three weeks in April.
“Machinic Domains,” curated by assistant professors Kory Bieg, AIA, and Clay Odom, and research scientist associate Benjamin Rice, with design and fabrication support from UTSOA students Philip Richardson, Bruno Canales, Holden Smith, and Rachel Deschner, showcases a small army of objects and armatures created through iterative explorations in robotic fabrication.
About 20 independent, knee-high assemblies blossomed about the gallery’s polished wood floor in a variety of vaguely organic configurations. At first glance, it was difficult to determine the underlying order of the sculptures, which are defined by black, splayed bases, bent steel rods, and three variously sized translucent HDPE shelves illuminated from below by sleek, low-profile chrome fixtures. Viewed collectively, the sprawling array seemed highly various but turned out to be composed of just three unique modules that achieved the appearance of difference through their aggregation. This discovery came as a surprise to viewers.
Like many exhibitions, the content presented was laudable for its captivating and enigmatic nature alone. But unlike many exhibitions, the content was perhaps the least exciting aspect of the show. That’s because the work is not an end in itself; rather, it represents a first step in showcasing a means to other ends that have yet to be identified or explored.
“The project is the beginning of something for the school,” says Bieg. “It’s really an investigation, not a stand-alone project. The process was one of unfolding discoveries, and this exhibition is more of a departure point for the future of fabrication and digital design.”
Bieg is broadly referencing the grant funding that the School of Architecture secured five years ago, which enabled it to expand its digital fabrication footprint. Most notably, the school acquired two floor-mounted KUKA KR 60 six-axis robotic arms, each capable of a 60 kg load capacity and a 2m reach. They also share a two-axis positioner, enabling collaborative work and increasing their combined handling potential to loads of up to 400 kg.
The addition of these tools complements the school’s already robust fabrication offerings, but the open-ended potential of the robots presents learning opportunities rife with possibilities. For example, unlike a traditional CNC router, the KUKA arms require custom tooling designed specifically for the task at hand. Specific “end effectors” attach to the robot’s arm and allow it to perform a distinct action. One end effector may be able to grasp a pen, while another may be suited to cold form steel. The design and integration of the end effector is just as integral to the robot’s ability to execute a given task as are the robot’s physical capabilities. Thus, the exploration of new fabrication techniques becomes less about the answer to “What can these robots do?” and more about “What tool can I design to make the robots do something new?”
This is the driving force behind Machinic Domains, and the work presented offers an exciting first glimpse of what we can expect from the school in years to come.
The assemblies are a departure from typical parametricism in that they use a series of uniform parts and repetitive processes to achieve their dynamism. The bases are black-painted MDF, routed by the school’s large-format CNC router. The steel frames are made from rods that are robotically bent as they move through dies, and are left raw to expose the texture changes that occur naturally as the material is manipulated. The shelves — or “petals,” as nicknamed by the team — are repurposed slabs of HDPE plastic that the school already had on hand in abundance and were fabricated on the CNC router. They were backlit by LED fixtures integrated into the displays.
The materials are held together by friction and slim, 3-D-printed fasteners. The assembly of the units was so specific and sequence-driven that the team didn’t even need to number or label any parts.
The petals themselves display a variety of smaller objects created through digital techniques and fabricated robotically, as well. These experiments explore processes of wax-melting, incremental forming of metal, drawing, and deposition or extrusion of caulk and silicon.
The exhibit’s aggregation was strategic, shaped by the desire to avoid site specificity and to leave the total number of units required open-ended. Analog studies were complemented by scripted studies in Grasshopper, a hybrid approach that seems well suited to the ethos of the school as a whole.
The exhibit notes that it serves as a demonstration project and also as an information warehouse from which students and faculty may begin their own investigations. As robotic fabrication and related disciplines only continue to gain relevance within the study and practice of architecture, Machinic Domains seems well positioned to launch the school into this emerging and exciting realm.
Christopher Ferguson, Assoc. AIA, is a designer at Clickspring Design and co-founder of DO.GROUP.
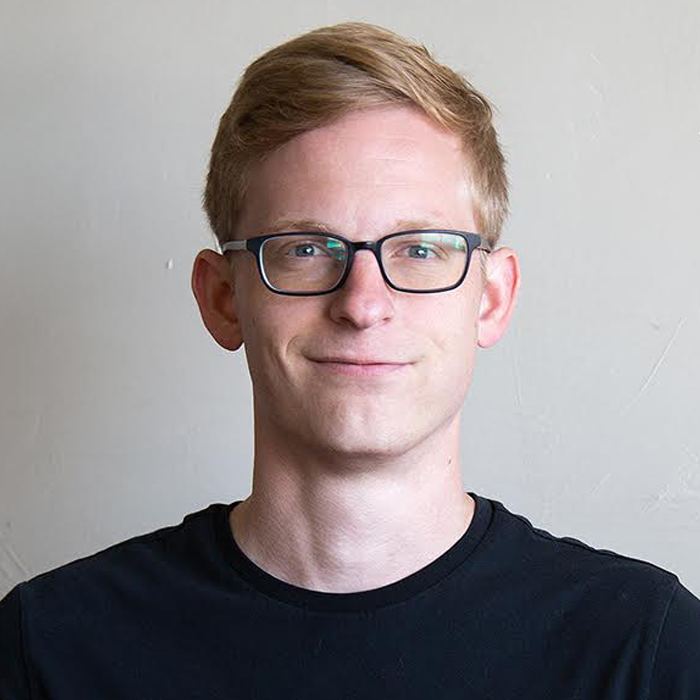